Electric trucks may not yet suit all applications, but urban devotees Dennis-Eagle are taking the lead. Trucking went to look at this silent revolution.
The past few years have seen tumultuous times in the haulage industry. From Brexit, through the driver shortage, the Covid pandemic and the massive increases in fuel costs. All have not only created exceptionally difficult operating conditions but have become divisive issues in their own right, adversely affecting all hauliers but those of differing sizes or different sectors in totally different ways.
Now, though, there is a new spectre on the horizon which is already polarising opinion far more than Brexit ever could: The electric truck. It’s not a temporary condition nor a passing phase; it’s coming, and it’s here to stay; that is the root of many hauliers’ consternation.
The much higher unit cost of the vehicles is one thing, the ‘refuelling’ infrastructure is quite another. It is less widespread than it needs to be, and the utopian ideal of fast-charging at a convenient point to coincide with mandatory driver breaks is just plain laughable. Rather than such a blanket insistence on electric traction – or hydrogen, for that matter – surely legislation should be in step with the practicalities. In one area, the industry is ahead of the curve.
Just like the first battery-electric commercial vehicle – the milk float – re-charging at the base overnight and running a full operating shift without recourse to ‘refuelling’ en route makes battery-electric a viable proposition. It is refuse trucks which are in the vanguard of this modus operandi and one of its leading lights is a UK industry success story.
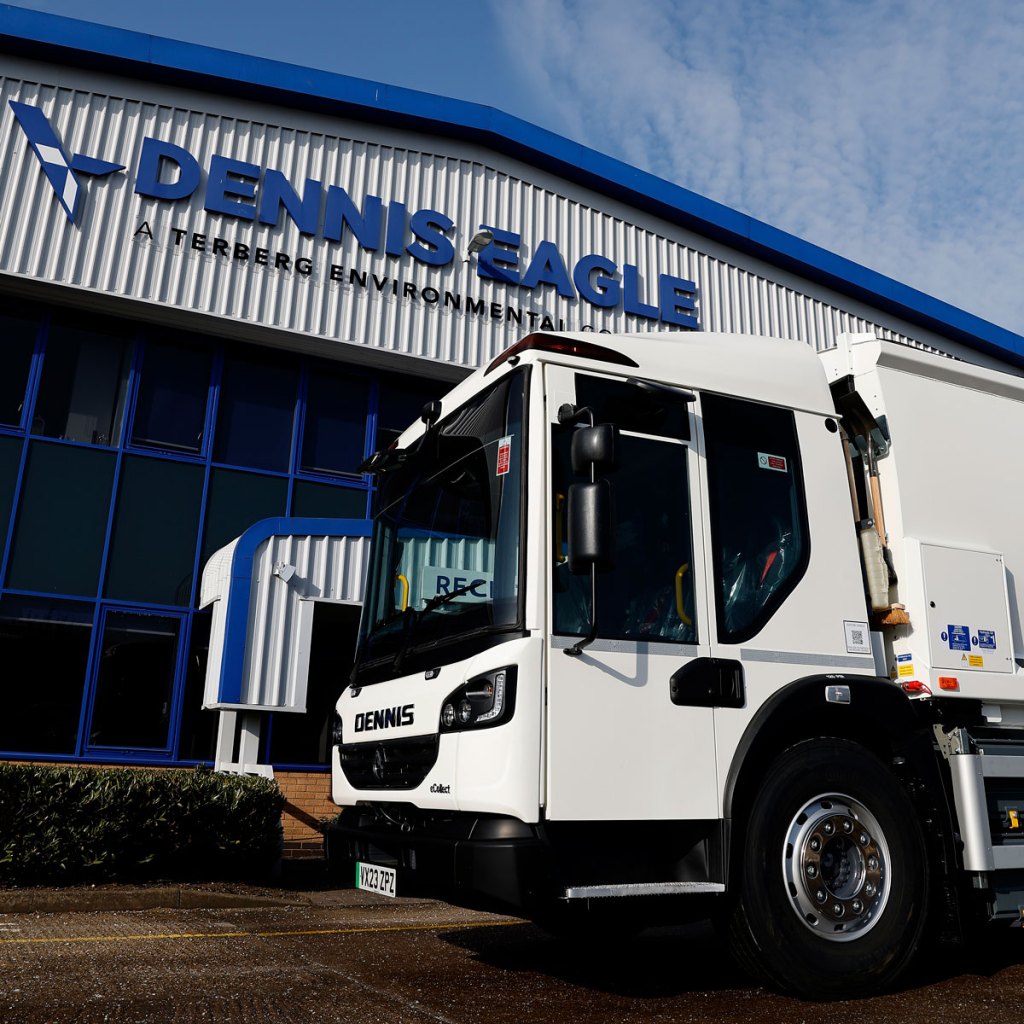
The future, now
It’s easy to get carried away with the futuristic aspect of electric vehicles – they were actually quite widespread (particularly in the USA) in the early 1900s – but the only real issue incumbent upon the vehicle itself is an increase in unladen weight brought about by the batteries.. At worst most commemorators feel this would warrant an additional axle at 44 tonnes to retain full payload and might see a wider adoption of 3-axle rigid / 4 axle trailer combo, so popular elsewhere in Europe. Otherwise it’s more of a conversion exercise, dependent upon the suitability of the existing chassis, although the very word conversion is to somewhat over-simplify the process.
Here, Dennis-Eagle is a strong position, historically a leading player in the refuse truck sector in its own right and stronger still as part of the Terberg Environmental Group, a world leader in the design and manufacture of refuse collection vehicles, it has been well-placed to take the lead with two all-electric versions of its most popular variants.
“The chassis rails are the same depth and the same distance apart as the diesel-engined versions,” explains Andy Graves, CRM, Data and Insights Manager, who is our guide around the factory today. Built on the most popular 3-axle 6×2 rear-steer chassis, the eCollect was first launched in 2018 with customer trials beginning in early 2019.
The first two production vehicles were delivered to Nottingham in 2020. That same local authority has just taken delivery of the 100th and 101st eCollect vehicles to leave the production line in Warwick, – the 4×2 eCollect had joined the line-up in 2022. Total output is around 32 vehicles per week, including 4 eCollect versions. With the same inboard dimensions and shared mounting points for cab, body and suspension components, the eCollect chassis only visually differs in the mounting brackets for ancillaries, with an obvious difference in the lack of fittings for diesel tanks, and the smaller electric pump for the hydraulics.
The drivetrain looks entirely conventional at this point, the bought-in Dana axles being identical to the single-drive two or three-axle eCollect derivatives or double-drive configurations, which to date are still diesel-powered. The imposed axle weights differ with the mode of propulsion. Where the diesel-engined four-wheeler utilises some ballast weighting of the front bumper area to balance out the tail overhang, the eCollect version’s traction batteries have a more centralised position, so this is far less of an issue, inherently keeping the axle weights equalised.
The power transmission does differ, however. Where the diesel vehicle employs a 5-speed torque-converter style automatic transmission, the eCollect has a one-speed gearbox. This system, common to the vast majority of electric cars and vans is a reduction gear, not only to reconcile the higher operating revs of the electric motor with a speed required at the propshaft, but having the added benefit of an equivalent increase in torque.
Nevertheless this is no mean feat for a three-axle rigid. Most electric trucks, and all electric artic tractors thus far, use a version of the current multi-speed automated transmission, so the eCollect removes some of that weight penalty. However, the proviso is that the eCollect does not need to maintain 56mph up hill and down dale all day and the original version had a top speed of 37mph. That was fine for urban work, but the larger motor now fitted, increases this to some 44 mph, which is a boon for rural authorities and matches the speed of the fastest class of agricultural tractor.
In itself not significant, but it surely opens up the Dennis-Eagle e-chassis to other utility applications as it already builds skip-loader, tipper and grab versions on the diesel-powered chassis, with the same high-visibility low-floor cab. The hydraulic system has a separate electric pump instead of a transmission PTO or engine-driven pump. It runs at a higher rpm than the PTO too making it more efficient into the bargain.
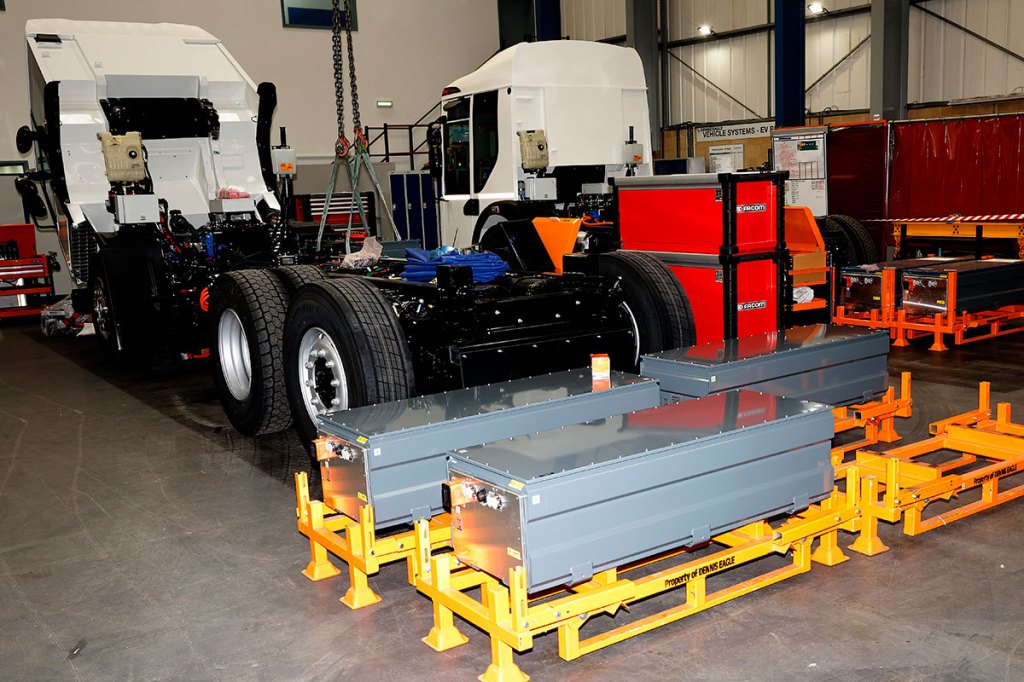
Forward Control
Further down the production line the cab is fitted. These are made in Blackpool on the site of the former Duple coach building works, “It makes sense to still build them in Blackpool,” says Andy Graves, “With highly skilled and experienced coachbuilders there, why re-locate or have to re-train staff”, he adds. It’s a doctrine that permeates the production facility here, of the 400 staff on site some 239 skilled workers are on the shop floor. The numerous model variants make robotised production unsuitable, it’s all hand built and even the cabs offer various options to customer preference. In a line of otherwise identical Elite-series cabs Andy points out the one with a flat roof, destined for New York.
The eCollect uses the Elite6 cab design, first introduced in 2015, as its packaging is better suited to this cab than the Elite+ design. Dennis-Eagle has been at the forefront of the low-entry design of cab for years with a height just 495mm off the ground, the one-step entry is poles apart from the loft-ladders of flat-floor tractor units. Not only does this make for easy crew access and egress but it puts the driver’s eye-level much closer to pedestrians, cyclists and other urban hazards. To this end, TfL (Transport for London) approached Dennis-Eagle to take part in the Construction Logistics and Community Safety (CLOCS) initiative.
This led to the development of an Urban Safety Vehicle range, which currently includes skip-loader, tipper and tipper grab variants, with plans to introduce a number of other body options. The Elite6 cab was independently tested in 2019 and found to provide the best direct vision of any truck on the UK’s roads, and the large glass area is immediately obvious from the outside, too, further enhancing safety as pedestrians can easily make eye contact with the driver. The flat floor is unobstructed for a true walk-through layout with Driver +1, +2 or +3 seating options applied to both standard and narrow width derivatives.
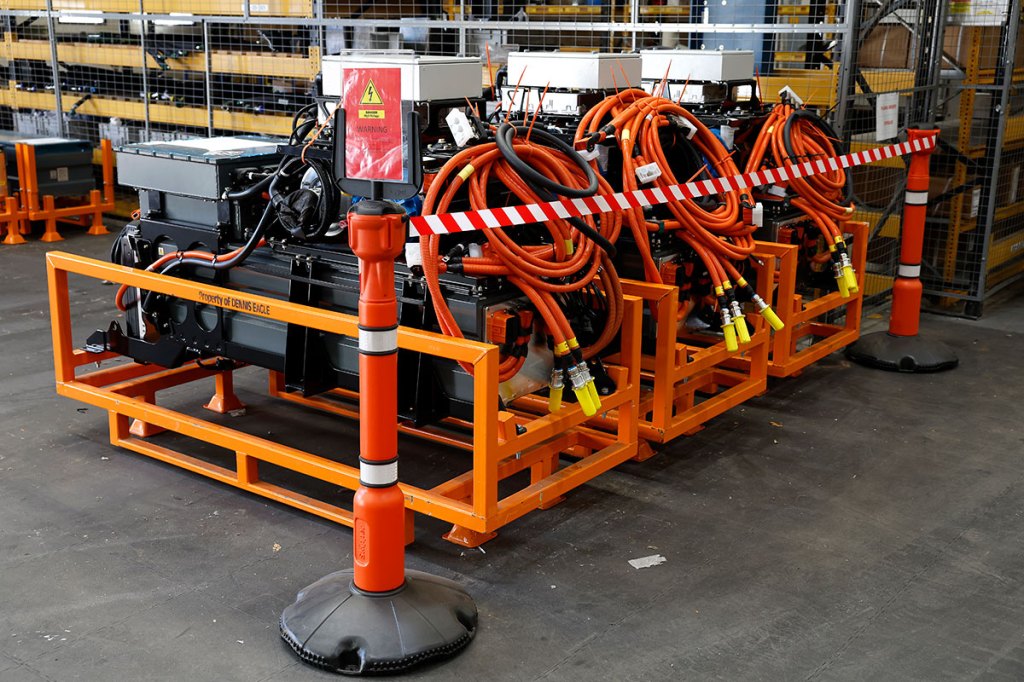
Powering up
Where the humble milk float had to make do with lead-acid batteries, the real advancements (indeed the key factor for EV acceptance) are in stable, fast charging Lithium ion batteries. The eCollect uses three battery packs in the 2-axle version and five on the 3-axle chassis, giving a total capacity of 180kWh and 300kWh respectively. Assuming an industrial-type 3-phase supply, a 50kW charger will take them from 25% charged to full in 3 hours 30 minutes, for the 4×2 or 6 hours and 45 minutes for the 6×2 version.
MAGTEC makes the batteries in Rotherham, a UK company which initially began in the prototype development of traction batteries and can now rightly claim to be the world leader in many new technologies within this automotive power source. Not only does battery power bring new challenges to the truck operator, it brings new safety issues to the truck maker too.
“Only qualified and approved members of staff can enter these areas,” explains Andy Graves as we reach the point where the electric truck meets its power source. Behind a cordon, the packs sit in protective stillages awaiting fitment. Dennis-Eagle has an excellent safety record and the advent of the EV won’t be allowed to affect that. The bright orange cables, a new automotive standard, indicate the high power feed to clearly differentiate them from familiar 12-24 volt red/black circuits. The batteries are substantial yes, but not huge, just visually comparing them to 12 volt lead-acid batteries with their tiny-fraction of power outputs, perfectly illustrates the pace of battery development and why it was so fundamental to the viability of EVs generally.
The next high voltage we come across is less restrained, arcing across from welding-wire to 8mm HARDOX-400 steel plate; this is the hopper-body fabrication line. The substantial structures are tang-and-slot aligned on jigs before the all-welded construction is completed by hand, no robot spot-welding here!
The body sections are then inspected and all joints have sealant applied to prevent corrosion, before heading into the paint shop. Although the company can paint in any shade the customer requires, the rise of vinyl wrapping means that the majority of vehicles leave the factory now in plain white. The wrap is not only easier and cheaper to apply, but it bolsters residual value too, since the second user – normally when the vehicle is five to seven years old – does not have to factor in a repaint. The paint quality is first-rate, it might never look this clean again but protection for the body’s unenviable task is important. The bodies are not just fitted to Dennis-Eagle chassis, around 8 bodies per week are fitted onto other makers’ chassis cabs, these being predominantly Mercedes-Benz Econics during out visit.
In the dispatch area it’s all Dennis-Eagles today with a mix of 2-axle, 3-axle and 4-axle versions. These double-drive plus rear-steer models are particularly well liked in Australia and four such chassis-cabs per week go down-under, for locally-built bodies to be added. Andy Graves spots an eCollect 6x2RS amongst them and after a quick sign-out of the keys, pulls it into the sunlight. It has that ‘new car’ smell in the wonderfully airy and specious Elite6 cab. A conventional park brake and push-button R,N,D along with the pleasantly curved two-tone grey and black dashboard and large diameter steering wheel actually puts one more in mind of a bus; must be the low eye-point and the huge glass house. A faint hum is all that accompanies the gentle ease-off into forward motion.
The main sensation is one of linearity, there’s no rise or fall to the sound like engine revs, whilst your brain waits for an automated gear change, which never comes. Nor does any emission. In an instant it’s so obvious that this has to be the future that you can only wonder why it took so long. Electric vehicles are all about the environment, but likewise the environment has to be right for the electric vehicle. This one is. Local operation, fixed operating radius from base and a known route.
The eCollect has the road speed, range and operating efficiency, for its intended environment. For all LGVs to go electric, nothing in the fundamental technology has to change, but a huge about the operating environment will have to; and soon.

Power take-up
Today, Dennis-Eagle manufactures over 1,000 units per year for UK local authorities and private sector contractors. In addition, it has a continually expanding customer base overseas, including in continental Europe, Scandinavia, Australia and the USA. The eCollect has gathered pace since its 2018 introduction with a number of council’s trialling them from day-one.
Cardiff Council held field trials of the eCollect on its own rounds in July 2020 and was among the first local authorities to place an order, putting its first eCollect into service in April 2021. By June it had ordered five more.
The Welsh Government helped with funding through an initiative to speed up the transition of local authority waste fleets from diesel to ultra-low emission vehicles.
Within the One Planet Cardiff plan, more than 100 council vehicles were to be converted to electric power in two phases. The council has also set up a 9MW solar farm – covering an area the size of 20 Principality Stadium pitches – on an old landfill site. The council’s One Planet Cardiff plan is aimed at driving the Welsh capital towards becoming a carbon neutral city by 2030.
July 2022 saw three 6×2 eCollects being operated by Exeter City Council’s fleet partner SFS as part of a seven-year fleet agreement, after extensive trials. As well as producing zero carbon emissions, the 27-tonne vehicles help improve local air quality by producing no nitrogen oxide or particulate emissions. To further reduce the council’s impact on climate change, the new electric fleet will be powered by the Water Lane Solar Park in Exeter. Many other councils, or their fleet partners, are trialling the eCollect and Dennis-Eagle is expecting the percentage of EV chassis to overtake its diesel vehicles in the UK before too long.
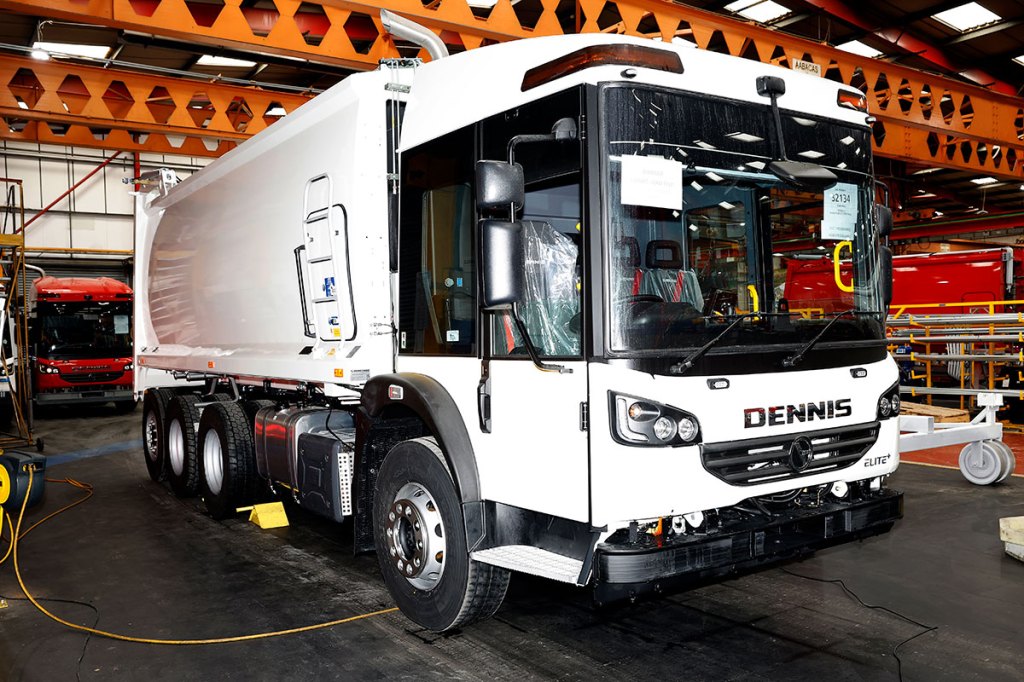
Specification
- Model: eCollect 4×2 narrow track
- Design GCW: 18,000 kgs
- Front Axle: 7,100 kg
- Rear axle: 11,500 kgs
- Unladen: 13,185 kgs
- Wheelbase: 3250mm
- 295/80 R22.5 tyres
- Motor: 200kW (268 bhp)
- Batteries: 180kWh
- Cab: Elite6
- Body: Olympus OL10N
- Model: eCollect 6x2RS narrow track
- Design GCW: 27,000 kgs
- Front Axle: 8,000 kg
- Rear axle(s): 19,000 kgs
- Unladen: 15,300 kgs
- Wheelbase: 5250mm
- 295/80 R22.5 tyres
- Motor: 200kW (268 bhp)
- Batteries: 300kWh
- Cab: Elite6
- Body: Olympus 19N
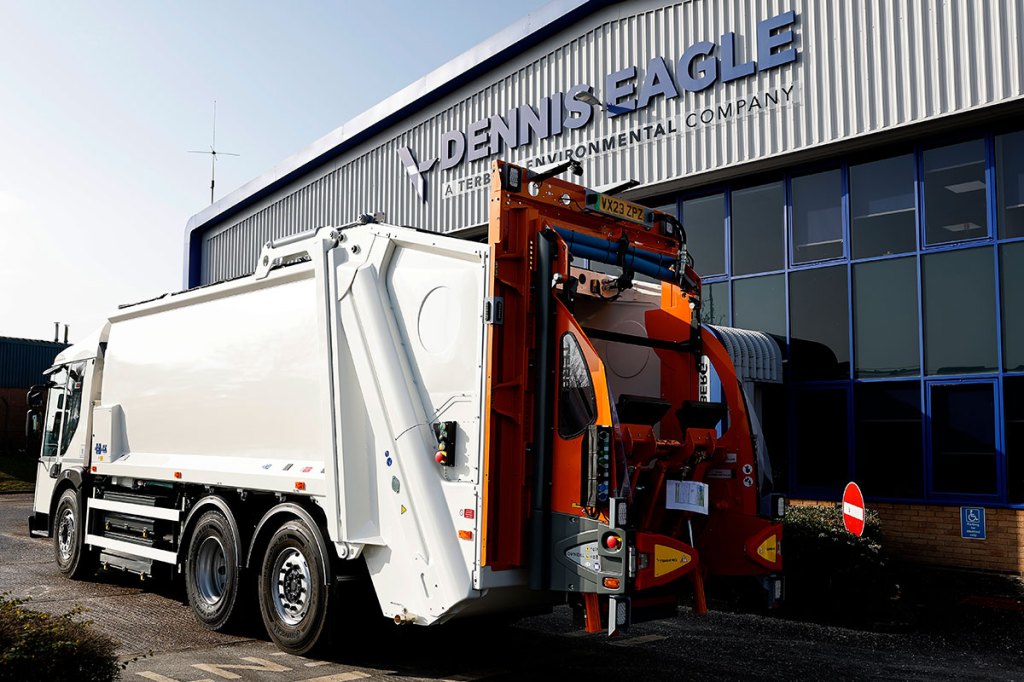